8.25 Roundtable Recap: Nemawashi
- Construction Progress Coalition
- Oct 14, 2021
- 6 min read
Updated: Oct 20, 2021
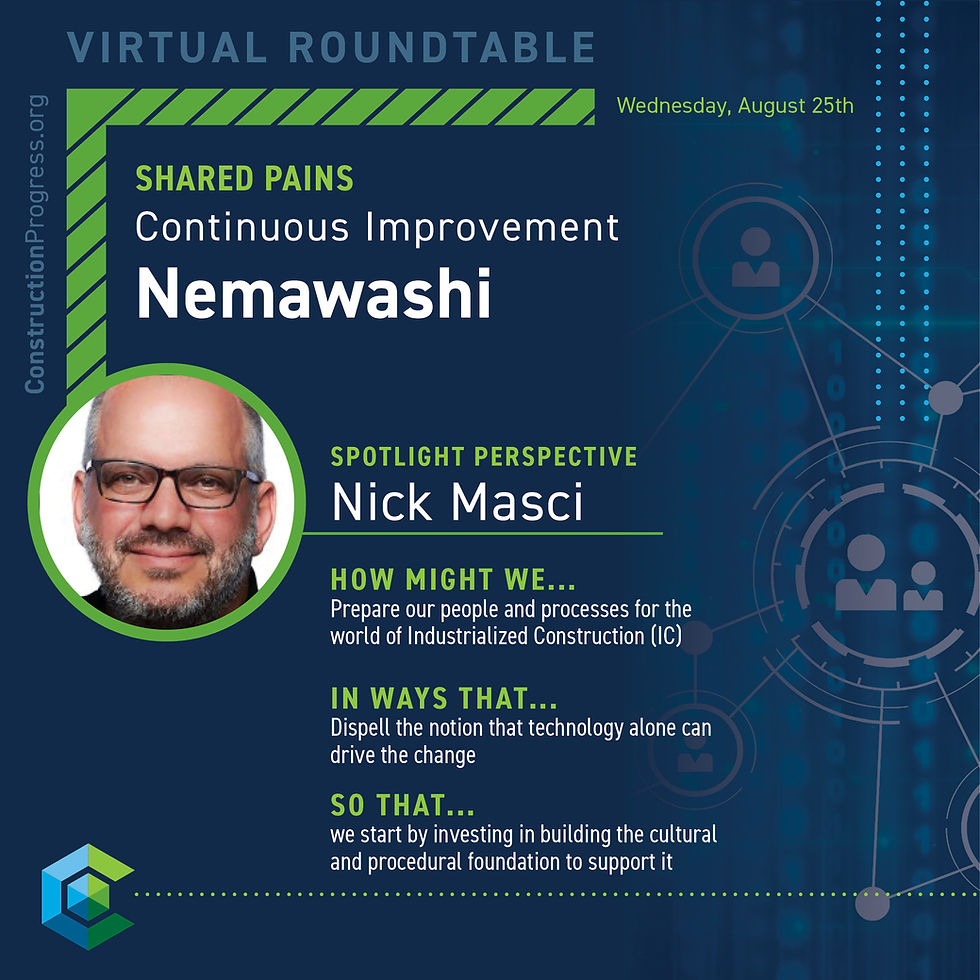
The Benefits of a Nemawashi Mindset
Nick Masci | Lean Coach for Industrialized Future, Haley & Aldrich
If there’s one thing people across the construction industry can agree on, it’s that surprises on a project are generally considered a bad thing. The more we know, the better off we are, right?
As a new member of CPC, I was surprised to learn that this primarily technology-focused organization maintains core values that start with caring for people before fixing the process. I found that many of the process improvement concepts we teach at Haley & Aldrich are directly aligned with princip
les of the common data exchange (CDX) framework. Similar to the value stream mapping (VSM) workshops I facilitate that grow from pictures of Post-it notes to elaborate Visio process diagrams, the CDX framework is meant to help project delivery stakeholders better communicate their data requirements in order to define better processes, together.
One Lean practice that has been critical to the success of any VSM workshops I facilitate is called “nemawashi.”
Loosely translated from Japanese, nemawashi is the act of “preparing the ground for planting so the roots can take hold.” In construction, we can equate this to the soils testing, excavation, shoring, and subterranean structural elements that precede the construction of the first foundation.
I believe nemawashi thinking can provide the same benefit I saw in my VSM workshops when applied to our CDX initiatives. Chad Pearson moderated a Continuous Improvement Roundtable on this topic and invited me to share my knowledge. In case you missed the discussion, here’s a summary of what we talked about.
Continuous Improvement is more than just a buzzword
It’s critical that the construction industry learns that the Lean buzzword “continuous improvement” is not simply about adopting new technology. Continuous improvement begins by building a foundation for success.
Despite all the recent excitement around Industrialized Construction (IC), the road to adoption has been long and slow. Technology and automation will help us build faster from a sound digital foundation. However, we haven’t done the necessary work to build that foundation in the first place.
Your digital foundation is not your technology, it’s your standard operating procedures (SOPs). And before those SOPs can be memorialized and communicated to the masses, they should be developed with respect for the people that they impact.
By laying the right foundation with empowered people who work together to define standard practices, transformation initiatives can begin to take hold. The same adoption pains that bring us together as CDX Delegates are also what bind together Lean practitioners… talk about #SharedPains!
Unpacking the nemawashi mindset
Nemawashi is a powerful tool to combat the “I'm too busy to change” mentality that is pervasive in construction. But too often, I see leaders disrespecting their teams when they essentially say, “do as I say, not as I do” when it comes to even simple things like preparing a meeting agenda. This kind of behavior is driven by a fixed mindset that doesn't see value in learning and continuous improvement. Nemawashi invites us to move from there to a growth mindset culture. We need to establish this culture to be set up for success in adapting and adopting new processes and tools.
This thinking doesn’t just apply to the fab shop or jobsite. Making time to document, review, and improve SOPs collaboratively can improve virtually any process. Take sales as an example. If you take the time to deeply understand a potential customer’s wants and needs, to really till that soil, it will yield a higher likelihood of landing the job.
Why having a nemawashi mindset matters
(hint: it’s our people)
When you apply nemawashi thinking, you pause to look at the situation on the ground as it stands. And that means sitting down with the people who interact with that problem on a daily basis. In fact, Lean thinking says that the people who do the work should be the ones to define the process.
And that makes sense because, at the end of the day, people come to do good work. What gets in their way are the processes. If you empower people to transform those processes — and give them the time to communicate and build consensus — you lay the groundwork for meaningful change. When the people doing the work can create or adapt the processes that affect them, you gain their trust and buy-in.
The main goal should be to make things easier on your people. This isn’t just nice. Easier leads to better, faster, and cheaper. Instead of chasing low-cost, chasing easy means the quality will be better the first time around. And that means things can happen faster. When higher-quality things are happening more quickly, overall costs come down.
Ultimately, this always comes back to culture. You can’t rush your way through nemawashi. You have to go slow at first to go fast later.
What’s holding us back
Nemawashi points to the root of our problems, but we could already see them popping through the soil. We give our teams automation solutions that are supposed to boost their productivity ten times over. But because the people don’t know how to use these tools, don’t have the right management systems, or lack good processes, the automation journey falters.
We often get caught up in the shiny new things on the industry stage, like:
Digital technology
Design for Manufacture and Assembly (DfMA)
Robotic Process Automation (RPA)
But before we can lean into these opportunities, we first need to get the core things right. We need to prepare the foundation. And that means putting work into:
Our core principles and cultural dimensions
Our management systems and leadership behaviors
Continuous improvement (our speed of learning)
This is preparing the ground. If we can get our core principles, leadership, and learning down, the production pieces will flourish.
Connecting nemawashi to CDX
I was excited to share my knowledge about nemawashi during this CPC Roundtable because it is so applicable to the path I see the CDX framework on. The same way teams prepare for one of my VSM workshops, nemawashi reminds us to step all the way back to ensure the scope of work you’re mapping includes all impacted perspectives.
Oftentimes, the solution cannot be solved within a single stakeholder’s narrow view of the supply chain. Instead, we have to broaden our field of view to include outside perspectives that may input, extract, or otherwise influence the reliable and efficient flow of information.
Our shared vision of a connected jobsite will be nothing more than a dream if we don’t start by getting the whole team involved upfront. Lean thinking asserts that people deserve to see and understand the systems they work in — and they’re best suited to solve the problems that arise there. Thankfully, BIM and other VDC tools give us the ability to do that earlier in the process and, in doing so, identify problems before they arise.
Where we go from here
These changes in workflow will ultimately disrupt the current state and create pushback. So, how do we address the natural human resistance to change? You guessed it: nemawashi!
Despite the clear differences when compared to construction, there is a lot we can learn from the manufacturing industry and their Lean adoption journey. They learned that a huge source of waste comes from not addressing quality issues at their source. By focusing on quality first and prioritizing it over production rate, they were able to hit a 99.5% inspection pass rate, which eventually led to faster production with little or no re-work.
In construction, when we talk about plan percent complete and inspection pass rates, we’re probably closer to 50% or 80%. Those measurements need to change, but they won’t until we set a new level of expectation.
Ironically, nemawashi requires us to “go slow” before we can “go fast” later. When someone comes forward with a problem, the goal is not to jump to a solution. Instead, nemawashi encourages us to make time to evaluate the current condition.
Flagging a defect and allowing it to move down the supply chain may help your company hit your daily production goal, but it creates ripple effects for everyone else downstream. So, instead of disrespecting those project stakeholders by providing poor quality on time, communicate the delay as soon as possible and perform a root cause analysis to prevent the delay from occurring in the future.
In order to keep up with the speed our clients demand and nurture strong relationships with our subcontractors, we need to simplify. We need to provide visibility, consistency, and accuracy, all while achieving the cost control required for our financial success. And all of that becomes possible with nemawashi.
So gather your team and look at your work environment. Is it prepared for growth? Or, is it covered in weeds that still need to be pulled? Who will be responsible for pulling the weeds and tilling the soil?
More and more industries are adopting Lean thinking. If you start working on this now, you’ll be poised to look attractive to owners who want to work with organizations that think like theirs and value continuous improvement. I hope to hear your thoughts in the comments below, or on a future CPC Virtual Roundtable!
Comments